View Pdf » EN
Low-pressure Compressors for Envases Universales in Merida, Mexico
Pneumofore Rotary Vane compressors have been running since 2020 for the low-pressure requirements of the 2-piece can manufacturing in the Envases Universales factory in Merida, Mexico. Following the tangible energy savings of these machines, a third 400 kW compressor was ordered to keep fulfilling the increasing production demand.
Within the high-speed 2-piece can manufacturing process, there are several production steps that require compressed air of 3,8 bar(g) or 55 PSI. In the past, it was common practice to run compressors at 7 bar(g) or 102 PSI and to reduce and adapt the pressure according to the production line request. Nowadays, power saving considerations strongly support the use of low-pressure compressors because they can drastically reduce the power consumption, almost cut in half, in comparison to standard 7 bar(g) units.
In 2020, the expanding Envases Universales group chose two Pneumofore A520.4 for the supply of low-pressure compressed air in its plant in Merida. Equipped with Variable Speed drives, these Rotary Vane units have a total installed nominal power of 800 kW. As the temperature in the compressor room can easily exceed 45°C, Pneumofore compressors were delivered in their Hot-Climate version to ensure long-term, reliable and constant performance even in extreme climate scenarios. Furthermore, Merida is close to the sea and the humidity is quite high, above 80%. Being exclusively air-cooled, the Pneumofore A520.4 HC air compressors are designed to run trouble-free and to perform well also in this harsh environment.
The customization required by the customer was applied also on the electrical panel, with the exclusive use of AB Rockwell components, including the 400 kW Variable Speed drive, the PLC for remote control and the HMI interface.
All major operation data from the compressors are available remotely in the central control room. Moreover, Pneumofore engineers supported the customer with the piping system layout. Pipelines and receivers are indeed key factors and they need to be sized correctly in order to optimize the distribution of compressed air without losses of pressure or capacity. The economic returns are remarkable, taking into account that compressors and vacuum pumps represent about 50% of the total power consumption within a modern 2-piece factory. With the production target of more than 3.000 cans per minute, many adjustments and improvements were taken in consideration by the plant management. Clearly, reducing the energy bill was a major objective and the use of customized compressors was crucial to achieve big energy savings.
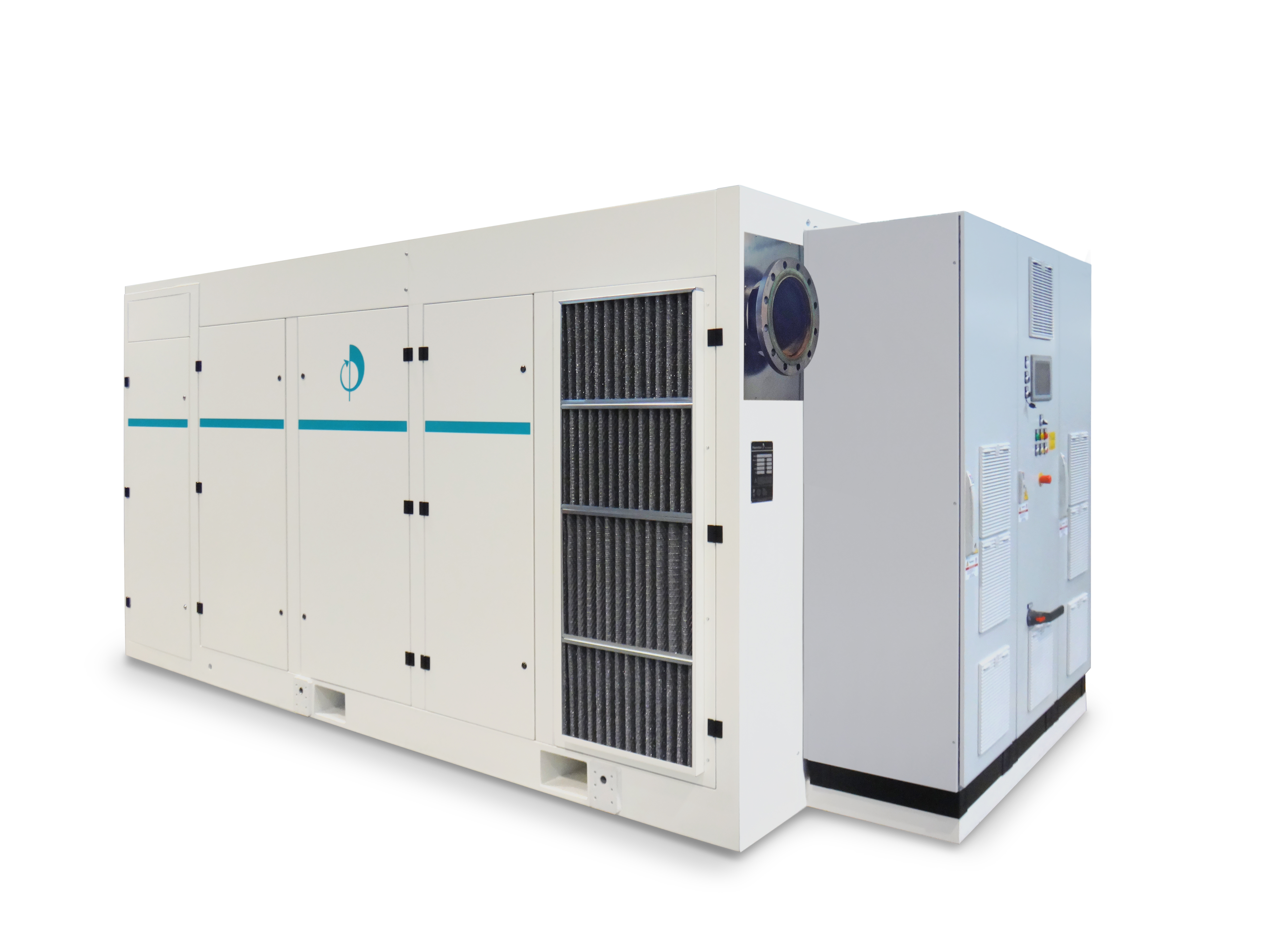
Pneumofore A520.4 VS400 HC Air Compressor
Pneumofore relies on a century of experience in manufacturing tailored compressed air and vacuum solution for the industrial sector. Thanks to the company commitment to its core value, the Rotary Vane technology has been researched and developed for a century and for the optimal long-term performance. There are Pneumofore units running non-stop in can factories for over 20 years. All they need is a correct annual preventive maintenance to achieve even a higher age of 30 or 40 years of trouble-free operation. Some older Pneumofore compressors are running round-the-clock since 1966.