Compressors in Mines
A special version of compressors was designed for the use in explosive areas. The rotary vane air ends allow lower temperatures, thus minor risk of fire caused by heat. Besides ATEX certification, the units were moved easily in elevators and tunnels of coal and salt mines to their installation location 700 m below ground level.
The rare presence of explosive gasses in underground mines is probably the cause of uncommon but extremely dangerous accidents. The precise reasons for explosions in mines, usually the cause of death of dozens of workers, is unclear. The compressors installed underground surely represent a danger due to their dissipated heat, moving parts and difficult accessibility for frequent service. Without mentioning the specific tragic events that moved Polish air compressor specialists to start the collaboration with Pneumofore, we can report now about the 7 years of continuous operation of our 20 rotary vane air compressors.
First, the compressors must fit on the narrow trains running in the 350 km of underground tunnels, at 700 m below ground level. The elevator is used to move on the different levels and the shape of the shaft is the first limitation for dimensions of transported goods. The standard compressor size is 75 kW unit running at 6 bar(g).
The previously used screw compressors were tailored made to satisfy the dimensional limitation, but showed excessive risk of explosion due to high temperatures caused by high speed of rotation and many moving parts. The temperature in a Pneumofore vane compressor with intensive oil injection reaches max. 125°C were the screw runs at 200°C. The 2 bearings of the vane air end with direct coupling replace the screw elements with gear box and the total of 10 bearings. Also the noise was reduced, when moving from screw to vane.
The electrical components, starting from electrical motors, all wires and the control/power panel itself must be ATEX certified. The presence of sparks, the ignition of explosions, represents the highest danger. Electrical connections are immersed in wax to avoid any spark. But also metals with high temperature can be the cause for fire, thus the air cooling must be dimensioned generously, as the air temperature in the tunnel is about 24°C with a 30% RH value.
The compressed air pipes are of DN300 and 50 km long. Pressure and capacity losses must be considered, also because of the difficult inspection for leaks in the poor light and uneasy environment with forced ventilation. The pressure losses were reduced by having the compressors near the spot of need, thus they can run continuously at 5,2 bar.
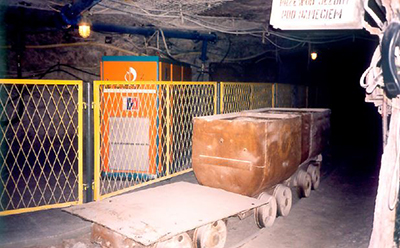
700 m below, running since 2002 @ 5,2 bar(g)
A considerable engineering work was done back in 2001 to design the AS75/V air compressor for underground mines. Today with units operating in Klodawa, Sobiesky, Pilsudsky, Ziemowit and Piast, Pneumofore can refer to precious references. The trouble-free operation results also from the intensive service executed by our local partners. Regular ordinary maintenance is important, as the accessibility for repair is restricted, reason why for this continuous operation the sturdy and reliable Pneumofore rotary vane air ends were installed.