-
home :404 SORRY, NO PAGE FOUND
404 SORRY, NO PAGE FOUND
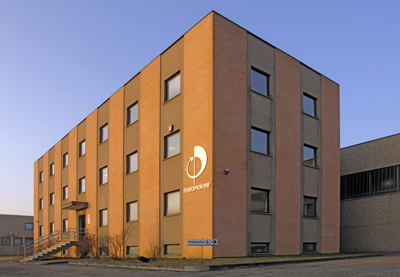
-
THE ROTARY VANE AIR END BY PNEUMOFORElargest air-cooled vane compressors and pumpsPneumofore leads the market with the largest single-stage rotary vane machines, both as standalone units
capable of up to 6,480 m3/h displacement, or in series for any size.simple, reliable & durableDirect coupling means few moving parts, low rotation speed, low temperature. This virtually eliminates repairs
and ensure superior reliability and longevity.low cost of operationLow maintenance, negligible repairs, high energy savings, and high reliability (no production downtime) make this the
least costly long-term option available today.THE ROTARY VANE AIR END
BY PNEUMOFORElargest air-cooled vane
compressors and pumpsPneumofore leads the market with the largest
single-stage rotary vane machines, both as standalone
units capable of up to 6,480 m3/h displacement,
or in series for any size.simple, reliable & durableDirect coupling means few moving parts, low rotation
speed, low temperature. This virtually eliminates
repairs and ensure superior reliability and longevity.low cost of operationLow maintenance, negligible repairs, high
energy savings, and high reliability (no production
downtime) make this the least costly long-term option
available today. -
ROTARY VANE MACHINES BY PNEUMOFORElargest air-cooled vane compressors and pumpsPneumofore leads the market with the largest single-stage rotary vane machines, both as standalone units
capable of up to 6,480 m3/h displacement, or in series for any size.designed for extremesTested and proven for high performance in desert and tropical climates and available for special requirements
like explosive gas or food safety.high energy savingsAir cooling through vertical layout, direct coupling, and intensive oil injection can result in up to 70% less power
usage than other systems.ROTARY VANE MACHINES
BY PNEUMOFORElargest air-cooled vane compressors
and pumpsPneumofore leads the market with the largest
single-stage rotary vane machines, both as standalone
units capable of up to 6,480 m3/h displacement, or in
series for any size.designed for extremesTested and proven for high performance in desert and
tropical climates and available for special requirements
like explosive gas or food safety.high energy savingsAir cooling through vertical layout, direct coupling, and
intensive oil injection can result in up to 70% less power
usage than other systems. -
PROCESS AIR TECHNOLOGY BY PNEUMOFOREfirst class supportEach unit come with integration engineering and a 5-year warranty. Extraordinary and regular service by
Pneumofore-certified professionals is available worldwide.low cost of operationLow maintenance, negligible repairs, high energy savings, and high reliability (no production downtime) make this the
least costly long-term option available today.designed for extremesTested and proven for high performance in desert and tropical climates and available for special requirements
like explosive gas or food safety.PROCESS AIR TECHNOLOGY
BY PNEUMOFOREfirst class supportEach unit come with integration engineering and a
5-year warranty. Extraordinary and regular service by
Pneumofore-certified professionals is available
worldwide.low cost of operationLow maintenance, negligible repairs, high energy
savings, and high reliability (no production downtime)
make this the least costly long-term option
available today.designed for extremesTested and proven for high performance in desert and
tropical climates and available for special requirements
like explosive gas or food safety.